As the application of pneumatic components in automated equipment and production lines becomes more and more popular, the working principle of the cylinder is to convert the pressure energy of compressed gas into mechanical energy in pneumatic transmission. operating units. Cylinder There are many types, and many users often do not select the correct cylinder type, resulting in unstable equipment operation and reduced cylinder life.
Cylinders are generally classified according to their structural features, functions, driving methods and installation methods.
According to structural characteristics, cylinders are mainly divided into piston cylinders and diaphragm cylinders.
According to the form of motion, it is divided into linear motion cylinder and swing cylinder.
Cylinders for reciprocating linear motion can be divided into single-acting, double-acting, diaphragm and impact cylinders. The single-acting cylinder has only one chamber that can input compressed air. The air is supplied from one side of the piston to accumulate energy to generate air pressure. There is only a piston rod at one end. The air pressure pushes the piston to generate thrust to extend, achieving movement in one direction. Its piston rod can only be pushed back by external force. Usually this will be done with the help of spring force, diaphragm tension, gravity, etc.
The characteristics of a single-acting cylinder are: only one end of the air intake, simple structure, small air consumption;reset by spring force or diaphragm force, part of the compressed air energy is used to overcome Spring force or diaphragm tension, thus reducing the force transmission of the piston rod;springs, diaphragms, etc. are installed in the cylinder, and the stroke is generally shorter;compared with a double-acting cylinder of the same volume, the effective stroke is smaller. The tension of the cylinder return spring and diaphragm changes with the deformation, so the output force of the piston rod changes during the process.
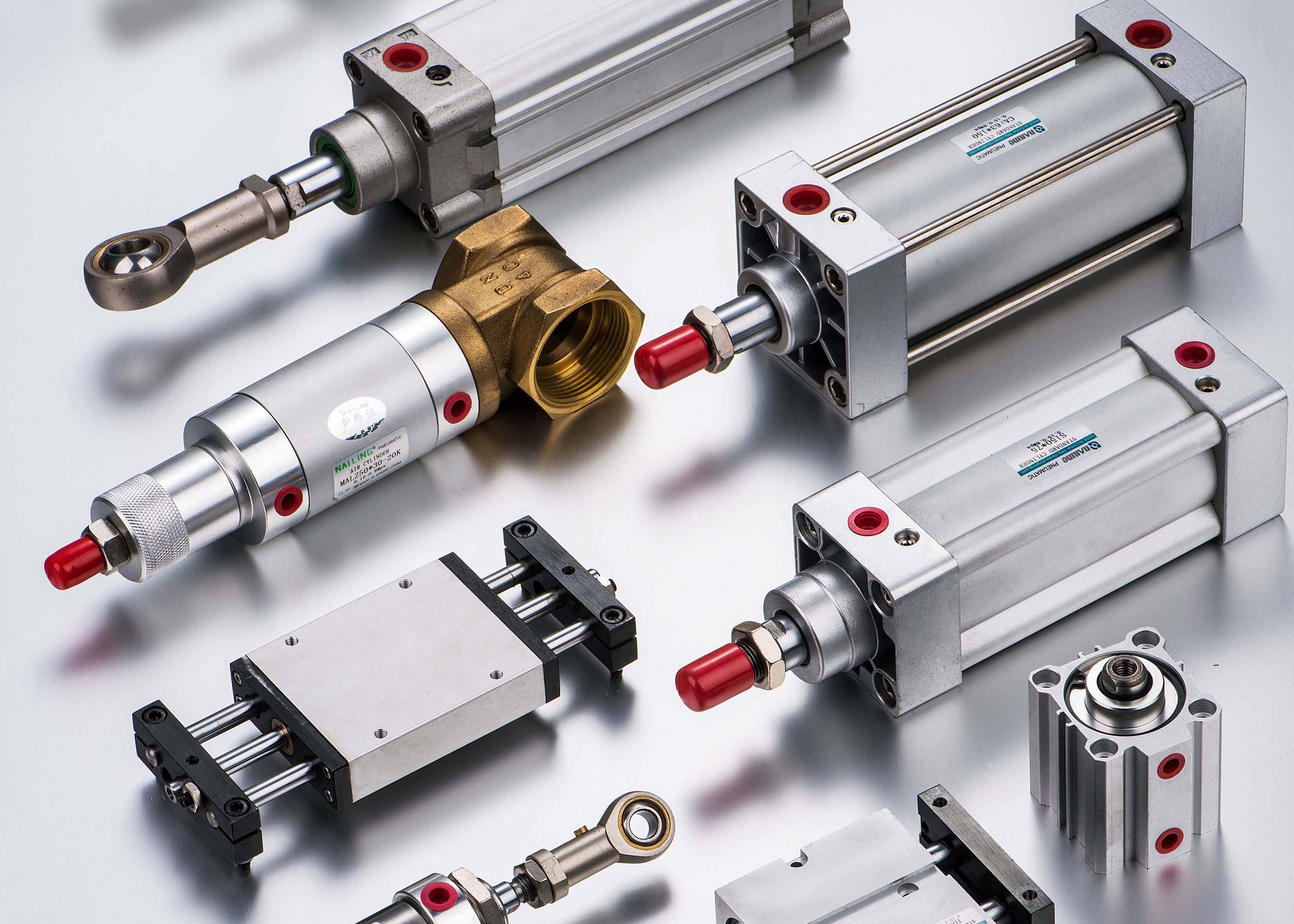
The correct selection of the type of cylinder in actual applications should be based on specific working requirements and conditions.
If the cylinder reaches the stroke end without impact and impact noise, a buffer cylinder should be selected;buffer cylinder usually refers to air buffer.
If light weight is required, a lightweight cylinder should be selected;
Requires narrow installation space and short stroke, optional thin cylinder;
With lateral load, optional cylinder with guide rod;
If high braking accuracy is required, a locking cylinder should be selected;
The piston rod is not allowed to rotate, and the cylinder with a rod that does not rotate is optional;
Heat-resistant cylinders are required in high-temperature environments;
In corrosive environments, corrosion-resistant cylinders must be selected;
In harsh environments such as dust, a dust cover needs to be installed at the extended end of the piston rod;
When no pollution is required, a no-oil or oil-free lubrication cylinder must be selected.
The specific cylinder types mainly include: angle rotating cylinder, rodless cylinder, pneumatic finger, mini cylinder, needle cylinder, etc.
In addition to specifications, models, materials, etc., there are two other crucial points that are often overlooked when selecting automated cylinders: the connection and sealing of the cylinder.
The connection of the cylinder is related to the working pressure of the cylinder, maintenance methods, installation and fixation methods and cylinder sealing. According to cylinder Choose the appropriate cylinder connection method according to the usage scenario to make the cylinder use safer and more efficient.
The above isAutomation cylinder types Analysis and type application analysisContent introduction. If you want to know more relevant information, please log in to Sunway Pneumaticwww.diancifa.cc.