First we need to disassemble the cylinder from the valve body. Starting from the covers of the two ports of the cylinder, completely disassemble the covers. When disassembling the piston, we need to pay special attention to the gear rack. direction, and then forcefully transfer the cylinder shaft clockwise, which can make the piston move to the outside quickly.
Close the valve hole and gradually ventilate it, and then use greater air pressure to completely push out the internal piston. When using this method, be sure to ventilate the pneumatic valve slowly and gradually, otherwise The piston will suddenly spurt out. This situation is very dangerous and may cause injury to the operator. Completely remove the blocking spring on the cylinder shaft. Then take out the cylinder shaft from the other end of the valve. After completing the above preparations, you can clean all the components inside the valve and add lubricating grease to the components. The key components to add lubrication are: the inner cavity wall of the cylinder, the piston sealing ring, the gear strip and the back annular piece. The gear shaft and sealing ring also need to add a certain amount of butter.
After adding grease to the pneumatic valve, it needs to be installed in the order of disassembly and the components in the reverse order. There are some matters that need special attention during installation. Be sure to pay attention to the gear strips. The assembly position ensures that when the cylinder is ventilated, the piston can quickly move to the position inside the cylinder.
After the piston is fully retracted, it is necessary to keep the notch on the gear shaft and the cylinder body in a horizontal direction. When the pneumatic valve is closed, the piston moves to the outside position. At this time, the upper part of the gear shaft The notch remains vertical to the cylinder body. The order and position of installing the valve must be clear. You must first understand the installation drawings and then assemble them. Prepare the parts that need to be assembled in advance. First check the parts to see if there are any missing parts. Place the parts on the work surface in a certain order. When assembling, make sure that each part is in its proper position and the direction of placement of the parts is also required. Stay Correct
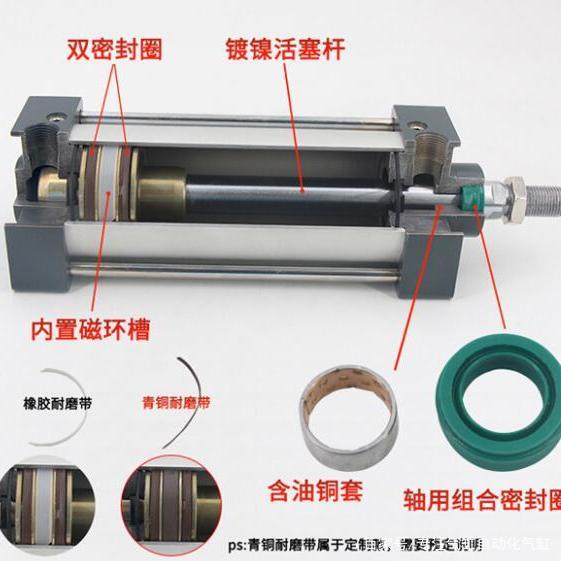
Causes and troubleshooting methods for cylinder air leakage
Cylinders will have problems and failures during the application process. A common failure is air leakage in the cylinder. Cylinder There are many reasons for air leakage. The following content is provided by the editor Let’s sort out several causes of air leakage in cylindersand their troubleshooting methods.
1. Several causes of cylinder air leakage
1. The piston rod is installed eccentrically or has scratches;
2. Insufficient lubricating oil supply and poor cylinder lubrication;
3. There are impurities between the piston rod and the seal;
4. There are impurities, aging, damage, etc. in the seals;
5. The threads of the four-tie-rod nut-type connection are loose.
2. How to eliminate cylinder air leakage
1. Reinstall and adjust, and retighten the connection between the cylinder block and the cylinder head
2. Check whether the oil mist device is malfunctioning
3. Clean and remove impurities
4. Repair or replace the piston rod
5. Replace seals